The last time I blogged about “The Terry” I had just finished the third top. Unfortunately a similar story developed for the back.
I originally had a beautiful piece of quilted maple for the back. The good news for quilted maple is that it is very beautiful. The bad news is that what gives it that beauty is that it is cut off-the-quarter (meaning the grain lines don’t run perpendicular through the wood). This is not usually a problem for violas and cellos but it can be a problem for violins depending on how stiff the wood is. As I was working this particular piece of maple, I just didn’t like the way it felt when I was cutting it. When I turned it over and started removing wood from the inside, I liked it even less. As a precaution, when I ordered the new top wood, I went ahead and ordered a new piece of maple as well.
I finished the back before my new wood arrived and when I went to tune the plate, the resonant frequencies were quite low and I still had some wood to remove. It was clear that this back was not going to work for a concert soloist’s violin. I believe it will make a quite nice violin that will be easy to play and will produce a wonderful warm tone, but it won’t have the power and projection required for someone of Terry’s skill.
So, when I finished the top for “The Terry”, I started the second back. It is a beautiful piece of maple but as I was working the outside, a small knot appeared. It was very small and wouldn’t affect the integrity or the sound of the instrument, however, on a one-piece back, some view it as character and others view it as a blemish.
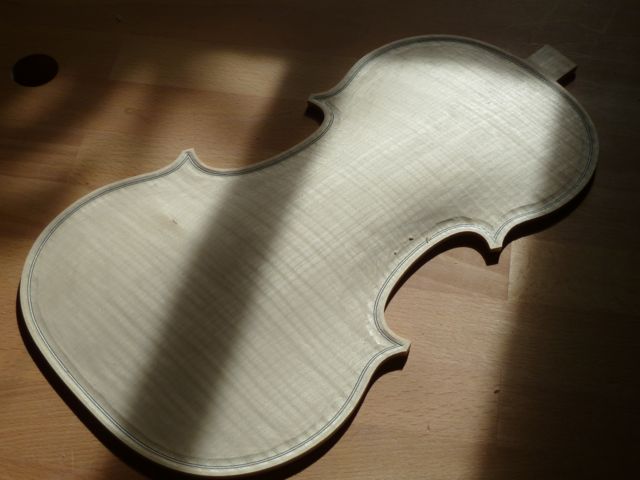
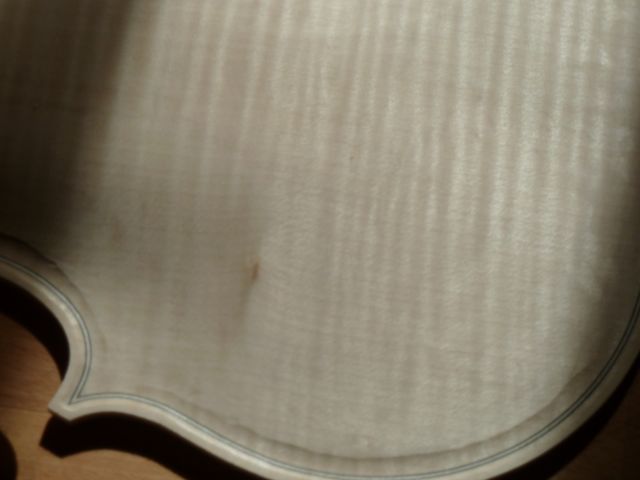
Unfortunately my time was up on Lummi Island and I had to head back to London. I stopped in Houston on the way and showed the back to Terry. She viewed the knot as a blemish. Because I guarantee 100% satisfaction, I agreed to make a new back.
That turned out to be a lot easier said than done. I asked my supplier in the U.S. to send me some pictures of their best quality one-piece backs. They had nothing I liked. When I got back to the U.K., I went to the two suppliers I use there, nothing (although I did find a nice cello back that I bought). I checked suppliers in France, Italy, Croatia, Slovenia, and Romania and still nothing. The biggest problem with the wood I saw was that it was grown in too warm of a climate. The summer grain was quite wide and I was afraid the the stiffness of the plate would suffer.

After checking with two more suppliers in Germany, I finally found a piece I liked. Andreas Pahler had a very nice one-piece back (I ended up buying a bunch of neck blocks from him as well). It finally arrived so I am back to work on “The Terry”!!!